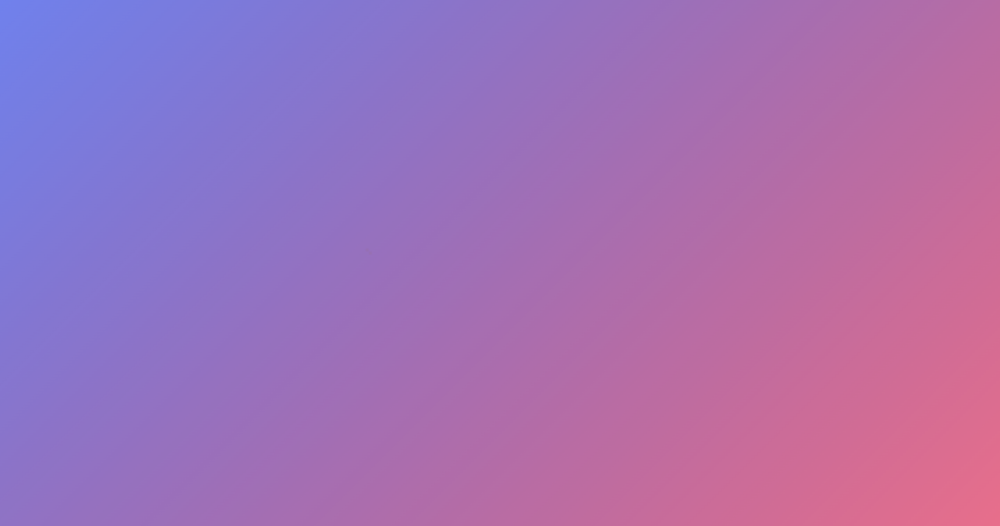
13
AprilSpeed Manufacturing: Reducing Setup Times
The ever-present challenge of manufacturing and production lies in the ability to efficiently manage diverse products. Historically, transitioning between tasks has been a time-consuming and labor-intensive process optimization an waste reduction. However, with the adoption of Quick Changeover, also known as Single Minute Exchange in Systems, this hurdle can be overcome.
Developed in the 1950s by a Japanese manufacturing genius, SMED is a approach focused on maximizing efficiency. The basic idea is to speed up the process of changing over while improving efficiency. This approach is centered on executing necessary steps to be executed before work arrives at the workstation.
The main target areas of SMED are optimization of execution. To implement this strategy, several key steps are taken:
1 Identify all the activities related to product changeover and categorize them into two groups:
those that can be done before the equipment/worker arrives at the workstation and essential activities be performed 'on the line.'
2 Using this division, optimize the preparatory activities, including removing machine guards, setting tooling up ahead of time, and even pre-assembling parts. This approach minimizes to a large extent the time spent on preplanned activities while the workers are on the production floor.
3 Once on the production floor, optimize activities that need to be done with immediate effect. This might involve optimizing workspaces, minimizing unnecessary movement, or performing simple construction steps.
Fast Changeover is not just restricted to manufacturing facilities but can be applied across various sectors where productivity are key to achievement. With SMED implemented successfully, production downtime significantly decreases, and businesses enjoy a boost in productivity, ultimately resulting in enhanced profit margins and customer satisfaction.
Reviews