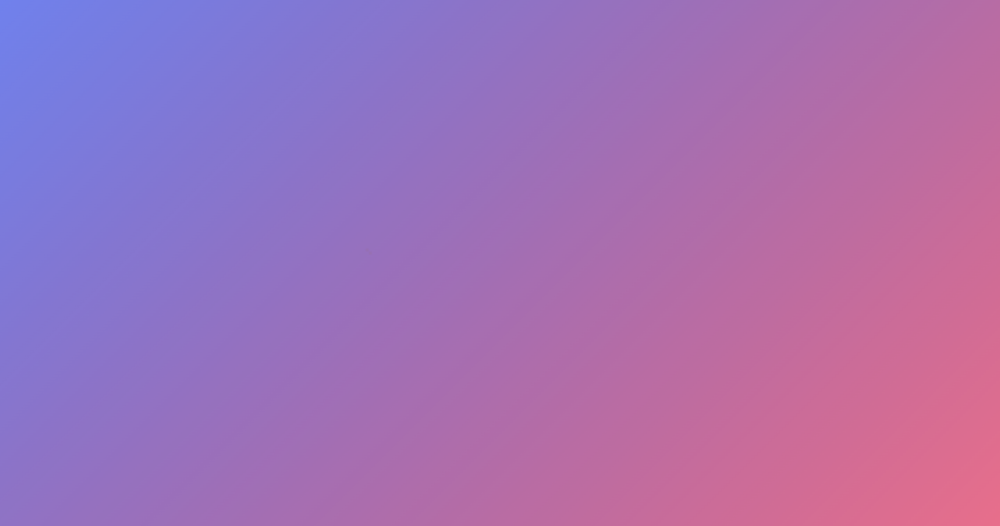
13
AprilMonitoring Process Stability
Control charts are a valuable monitoring system used to analyze data and detect trends by tracking and analyzing data. They were introduced for the first time by Walter Shewhart in 1924 and are still widely used today in finance.
A control chart typically consists of a graphical representation of the data collected over time, with the mean plotted on the chart. The chart has three key zones:, the central line which indicates the central tendency, the upper control limit which indicates the optimal range, and the lower limit which represents the lower limit of acceptable variation.
There are several control chart options, including:
- X-bar Chart: This chart is used to monitor the average value of a process over time. It is typically used for continuous data, such as scientific measurements.
- R-chart: This chart is used to study variability of a process over time. It is typically used 5S for improvement numerical data, such as scientific measurements.
- P-chart: This chart is used to study ratios of defective items in a process over time. It is typically used for qualitative data, such as quality metrics.
- C-chart: This chart is used to count defects of defects in a process over time. It is typically used for qualitative data, such as quality metrics.
To use a control chart, you need to follow these steps:
1. Collect data: Collect data from the process over time. The data should be reliable and representative of the process.
2. Calculate the mean: Find the average of the data.
3. Calculate the control limits: Calculate the upper and lower control limits based on the mean.
4. Plot the data: Plot the data on the monitoring system, using the mean as the central line.
5. Interpret the results: Analyze the data of the control chart. If the data meets the specified criteria, the process is said to be in control. If the data exceeds the specified limits, the process is said to be out of control.
There are different control chart warnings, a point or a run of points outside the specified ranges, either above or below the centerline. It can also occur when there are multiple sequential data points outside the designated range from the centerline, which is known as a shift in the process mean.
The control charting benefits has several advantages, including:
- Early detection of process problems: Control charts can identify issues promptly, allowing for quick action to be taken.
- Improved process stability: Control charts help to improve process stability by resolving issues.
- Reduced variability: Control charts can minimize variability in a process by identifying and addressing the causes.
- Improved quality: Control charts can enhance the quality by identifying and resolving issues that can affect the quality of the final product.
Reviews